On YouTube, you can find a video called “Golden Gate Bridge: All Destruction Scenes.” Watch it, and you’ll see the famous suspension bridge destroyed in a variety of ways: taken down by a giant octopus, melted by a lack of magnetic force from the Earth’s core (shown in image), crumpled due to a major earthquake, wrecked by Godzilla, collapsed by an alien probe, and smashed by a Sharknado. While none of these events are likely to happen to a bridge near you, there is an element of truth to these scenarios: bridges are vitally essential and vulnerable infrastructure, and if they are destroyed the consequences can have monstrous effects on bridge users—and the budgets of bridge owners. It doesn’t take a rampaging sea creature or a global natural hazard event to compromise structural integrity: normal wear and tear, like weather and vehicles, will do just as well.
Because of this, bridges need to be monitored for their structural health to make sure they can safely support the traffic that uses them. A bridge’s use can be quantified by its average daily traffic (ADT), or the number of vehicles that pass over the bridge per day; this number is often annualized (AADT). San Francisco’s Golden Gate Bridge, a 1,208-meter suspension bridge, has an AADT of more than 100,000 vehicles; closer to the Lehigh campus; in comparison, Easton’s Gene Hartzell Memorial Bridge, a 540-meter steel truss bridge, has an AADT of 59,000. To make sure bridges are safe, the Federal Highway Administration’s National Bridge Inspection Standards require a visual inspection every two years. But fixed sensors can be expensive and cumbersome, involving specialized equipment.
There are more than 600,000 bridges in the United States (about 32,000 in Pennsylvania). As of 2021 data, 42% of these structures are at least 50 years old, and 7.5% are structurally deficient. And the scale of repairs is daunting: remediation of all these structures would cost an estimated $125 billion and take decades to accomplish. And that’s before considering the bridges that will need repairs during those decades.
Lehigh University Department of Civil and Environmental Engineering doctoral student Liam Cronin, and his advisor, Shamim Pakzad, Professor and Chair of Civil Engineering, plus Cronin’s fellow graduate students, is working on a different approach to testing the structural health of bridges. Instead of using a visual inspection, this approach uses vibration frequencies collected via smartphones that accompany almost every driver as they travel over bridges and roadways. The basic principle rests on the vibrations that a bridge emits when vehicles pass over it. You might be surprised to learn that smartphones can collect vibration data, but it also makes sense. Your phone has a variety of sensors that make it user-friendly, whether for directions with GPS or through an accelerometer that knows when you turn your screen to watch a movie. For bridge monitoring, the same accelerometer is being used to measure the bridge’s vibrations and the GPS for the location of the car on the bridge. In most cases, these changes due to vibration are small. And the ubiquity of smartphones allows for copious data collection. (Download a vibration app, such as Gauges or Vibration Meter, to see your own measurements.)
A recent paper co-authored by Cronin explains the method behind this research. Data collection via smartphone is triggered when the vehicle carrying the phone enters a geofence (established by the researchers) that defines the bridge’s parameters. Everyday traffic over the bridge provokes vibrations, providing a structural response. The bridge moves to some degree because of the car’s weight, cars hitting potholes, and the environment, and that movement is sensed and recorded by smartphones within the passing vehicles. The smartphone data is processed according to the algorithms defined by the team, packaged, and sent to cloud storage.
Cronin and his colleagues use the collected smartphone data, primarily acceleration and location measurements, from many devices and then average out the measurements. (Currently, their data comes from researchers, and in some cases, solicited from Uber drivers.) They rely on such averages because the road surface and measurement noise obscure the bridge vibrations; the averages help manage the influence of, say, bad shocks or a pothole. At certain times, the researchers signal their servers to process the data, which involves, in part, generating graphs according to algorithms created by the researchers.
These graphs represent absolute mode shapes (AMS) and are one facet of the structural analysis. Researchers identify a reference graph for a bridge as the basis for future comparisons and compare them to AMS over time. Some of the properties the researchers look for with vibration-based monitoring, Cronin says, are vibrations occurring at different frequencies and vibrations that create different graph shapes. The changes indicate that something about the bridge has changed–it could be a health issue or something more benign. This approach allows for passive real-time data bridge monitoring, which, over time, can alert bridge owners to anomalies in the AMS graphs, and alerts them to the need to perform a closer physical inspection of the bridge.
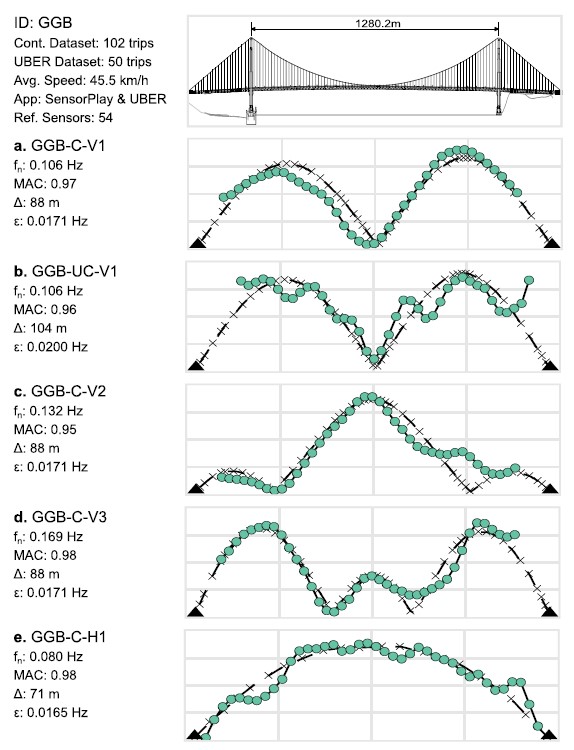
In fact, Cronin used data for his study of San Francisco’s Golden Gate Bridge that was gathered by his advisor, Shamim Pakzad, during his dissertation work on wireless sensor networks in structural health monitoring. Cronin’s work builds on Dr. Pakzad’s, and on the work of other students who have worked with him. Researchers in Cronin’s lab have analyzed data from several bridges of different types and lengths to see how it works on differently constructed structures. These include the Golden Gate Bridge, San Francisco; Gene Hartzell Memorial Bridge, Easton, Pennsylvania; Cadore Bridge, northern Italy; and Ciampino Bridge, Rome, Italy. This variety of bridge types, from suspension to steel truss to steel rigid arch to reinforced concrete, and their different levels of flexibility, lengths, and average daily travel load provides insights into each type as well as demonstrates the adaptability of the method. As Cronin says, the variety of bridge studies shows the scalability of the approach.
Work is still firmly in the research stage and is not yet ready to be deployed for public or commercial use. When it is ready to be implemented as a structural health monitoring tool in the real world, it will allow for accurate, easily implemented, and cost-effective passive monitoring. And such monitoring may be useful in disaster response, as when a Sharknado or non-shark hurricane hits a bridge, and in continuous monitoring, when the bridge is subject only to normal stress.
Cronin has co-authored articles focused on machine learning with a few of Pakzad’s other students, including Thomas Matarazzo, now an assistant professor at the United States Military Academy at West Point, and Soheil Sadeghi Eshkevari, Structural Engineering, who is now at Uber. Both Matarazzo and Eshkevari have worked at MIT’s Senseable Cities Lab, which uses multi-disciplinary approaches to solve problems in urban areas, and has also researched smartphone-based sensing.
Currently, Cronin is working with his father, Michael Cronin, a noted builder of recording studios and audio facilities in his hometown of Nashville, Tennessee. He’s still helping his Lehigh colleagues, too, by driving over bridges in Nashville to collect data on his smartphone during his workday. Despite his work hours, Cronin plans to have his PhD completed and graduate in spring 2025. And maybe in a few years, someone will be using his bridge vibration data to validate bridge structures, continuing Pakzad lab tradition. And to keep bridge collapses on the silver screen, not in everyday life.